Jump to Section:
Custom Injection Molds
Why Choose Us
Pipe Fitting Mold Specialists
Our Experts
Our team is proud of their skills in using advanced injection molding equipment which enables them to provide customers the economy of mass production regardless of the quantity supplied. Each day we meet the challenges of a demanding market in the rapidly changing thermoplastics industry.
While we specialize in injection molds for pipe fittings and PVC applications, we also offer a wide range of expertise in the design, engineering and building of all types of molds, using a variety of mold building steels. ESTERLE makes injection molds for all plastic part applications, including structural foam and compression molds for all products used in all industries. In addition, ESTERLE is able to qualify injection molds and offer short/long production runs at our location by using our own 7 injection molding machines ranging from 90 ton to 2600 ton.
PVC Molds
Designed To Work Harder
Save Money Without Sacrificing Quality
At ESTERLE, we understand that being one of the best in the industry isn’t always enough. We’ve also got to help you manage your production costs. By reducing cycle times and staying up-to-date on the latest processes for lean manufacturing, we’re able to stay competitive and keep you competitive too!
The production of PVC molds requires specialized steels to ensure longevity as well as requiring more tooling maintenance than those used in processing standard plastics. At ESTERLE, all of our PVC molding is created with the highest quality and attention to detail possible using methods we have perfected over the years.
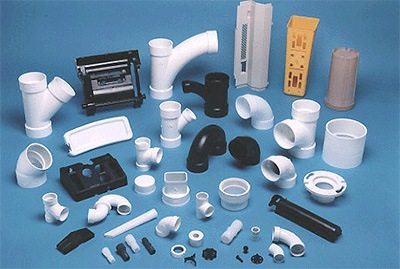
Collapsible Core Molds
Making Life Easier
Mold Sampling
What Makes Us Leaders
3D CAD/CAM
Streamlined Design Process
Enhanced Productivity
Our Software Allows For
Dynamic Molding
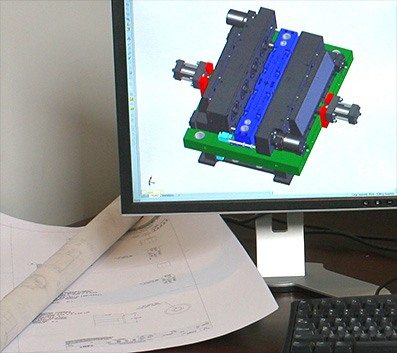
Mold Qualification
ESTERLE offers exacting in-house mold qualification and process validation – so that our customers are assured of consistent product performance before the equipment is assembled on their production floor and integrated with existing manufacturing systems.
We offer mold try-out, qualification, and part production using our own sixteen state of the art injection molding machines ranging from 90 to 2600 ton. For larger forged tooling and machining needs, we offer both large modern CNC and manual horizontal boring mills, as well as vertical machining centers.